Medical cable Assembly differ from other industries’ cables in several key ways. Here’s a detailed breakdown of the differences:
1. Biocompatibility
Medical cables must be made from materials that are safe for human contact. Unlike cables in other industries, they must meet strict biocompatibility standards to avoid causing irritation, allergic reactions, or infections when used on or inside the human body.
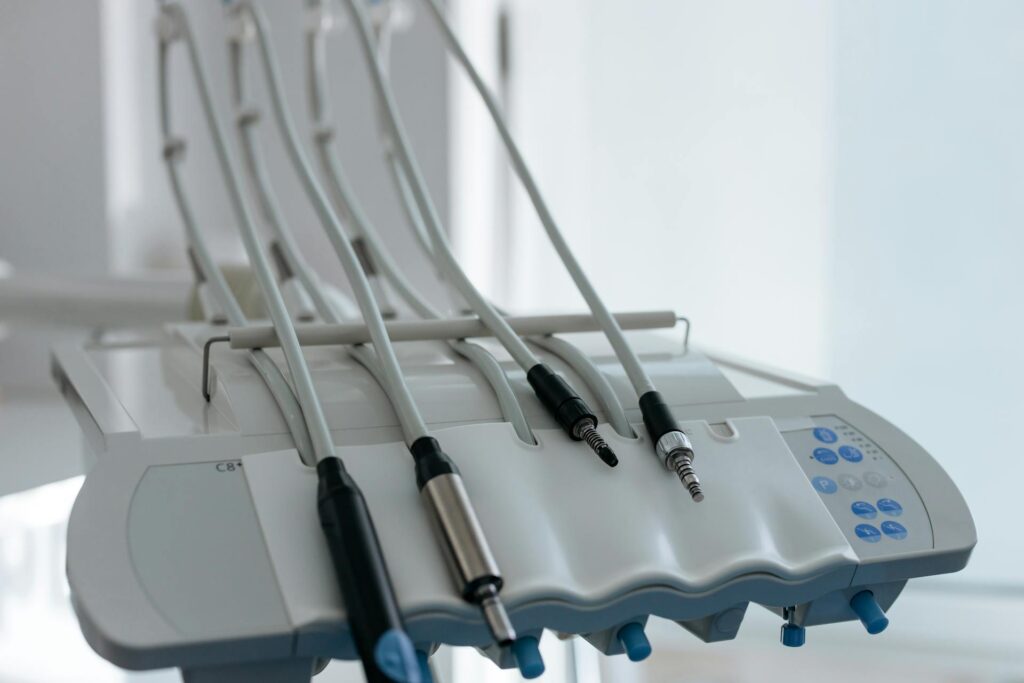
- Example: Cables for ECG machines require special coatings that won’t irritate the skin or degrade when exposed to bodily fluids.
2. Sterilization Requirements
Medical cables need to withstand repeated sterilization processes, which can involve exposure to high temperatures, chemicals, and moisture. This makes them more resilient compared to industrial cables, which are rarely subject to such cleaning protocols.
- Example: Surgical cables must be resistant to autoclaving, a high-temperature sterilization method.
3. Precision and Signal Integrity
Medical devices often deal with highly sensitive signals that require precise transmission without interference. Medical cables are designed with enhanced shielding and insulation to prevent electromagnetic interference (EMI), ensuring accurate readings.
- Example: Imaging equipment like MRI machines relies on flawless signal transmission for clear diagnostic images.
4. Durability and Flexibility
Medical cables are designed for repeated handling in demanding environments. They often feature reinforced jackets, strain relief mechanisms, and flexible designs to withstand frequent movement, bending, and pulling.
- Example: Patient monitoring cables must endure constant repositioning without breaking or losing signal integrity.
5. Regulatory Compliance
Custom medical cable assembly must comply with stringent regulatory standards set by organizations like the FDA, ISO, and IEC 60601 to ensure they are safe and reliable for medical use. These regulations are much more rigorous than those in most other industries.
- Example: Medical cables used in life-support systems require certification that they won’t fail under critical conditions.
6. Lightweight and Patient-Friendly Design
Medical cables are often designed to be lightweight, flexible, and comfortable for patients during use. This focus on user comfort is unique to medical applications, as other industries prioritize durability and performance over ergonomics.
- Example: Cables used for wearable medical devices need to be lightweight and discreet for patient mobility.
7. Resistance to Fluids and Chemicals
Custom medical cable assembly are designed to be resistant to bodily fluids, cleaning agents, and disinfectants. They must maintain performance even when exposed to these substances, unlike industrial cables that typically don’t require such protection.
- Example: Ventilator cables need to withstand frequent cleaning with harsh disinfectants without degrading.
Comparison Summary Table: Medical vs. Other Industry Cables
Feature | Medical Cables | Other Industry Cables |
---|---|---|
Biocompatibility | Required | Not required |
Sterilization | Must withstand repeated sterilization | Rarely required |
Signal Integrity | High precision, low EMI | Varies by application |
Durability | Flexible and highly durable | Durable but less flexible |
Regulatory Compliance | FDA, IEC 60601, ISO standards | Varies by industry |
Lightweight Design | Essential for patient comfort | Not a priority |
Fluid Resistance | Must resist bodily fluids and cleaning agents | Not typically required |
About Darlox (Zhijian) Custom Cable Assembly
Darlox (Zhijian) is a leading manufacturer specializing in custom cable assemblies for a variety of industries. With years of experience and a commitment to quality, Darlox provides tailored solutions that meet the unique needs of its clients. Their expertise spans across sectors such as automotive, medical devices, telecommunications, and industrial automation.